Цели разработки двигателя N52:
- Новаторские решения
- Компоненты базового двигателя
- Магний – новый материал в двигателестроении
- Конструктивное использование магния
- Нижняя часть блока цилиндров
- Электрохимические свойства магния
- Физические свойства материалов
- Обработка магния резанием
- Правила при обработки резанием
- Уплотнения
- Резьбовые соединения
- Система газообмена VALVETRONIC II
- Управление нагрузкой
- Устройство/принцип работы
- Привод клапанов с изменяемым ходом II в Н52
- Фазировка
- VANOS
- Масляный насос с регулированием расхода по объему
- Преимущества масляного насоса с регулированием расхода по объему
- Принцип работы масляного насоса с регулируемым расходом по объему
- Электронный контроль состояния масла
- Электронный контроль уровня масла
- Система охлаждения
- Насос охлаждающей жидкости с электронным управлением
- Управление теплом
- Интеллектуальное управление теплом расширяет возможности двигателя и пользователя
- Сравнение систем охлаждения с механическим и электрическим насосом охлаждающей жидкости
- Трехступенчатая раздельная система всасывания (DISA)
- Описание функционирования резонансного наддува
- Цифровая электронная система управления двигателем (DME) MSV70
- Принцип работы цифровой электронной системы управления двигателем (DME)
- Лидирующее положение за счет эффективной динамики;
- Увеличение мощности и крутящего момента;
- Снижение расхода топлива;
- Снижение массы;
- Технические новинки для удобства клиентов;
Легче всего было бы достичь этих целей за счет снижения массы двигателя. Уже в начале разработки M50 постоянно предпринимались попытки введения усовершенствований и использования новаторских решений, целью которых являлось обеспечение все более и более низкого расхода топлива при одновременном увеличении мощности и улучшении динамики.
В сравнении со своими предшественниками M54/M56, двигатель N52 отличается снижением расхода топлива на 12 % и повышением динамики на 10 %. И это при соблюдении строгих европейских и американских норм токсичности ОГ – EU4 и ULEV II.
При разработке N52 были так же приняты во внимание следующие требования клиентов и законодательства – повышение комфорта, снижение выбросов и улучшение соотношения стоимость/эффективность.
Для того чтобы иметь возможность сравнивать между собой отдельные силовые агрегаты, были введены понятия литровой мощности и удельной мощности. Величина литровой мощности характеризует наибольшую полезную мощность, которую развивает двигатель на литр рабочего объема [кВт/л]. По сравнению с M54, на двигателе N52 удалось повысить ее с 55 кВт/л до 61,7 кВт/л.
Удельная масса обозначает массу двигателя, приходящуюся на один киловатт его мощности [кг/кВт]. Чем меньше масса двигателя по отношению к его мощности, тем более эффективной становится отдача мощности. В плане удельной массы N52 также задает новые масштабы. По сравнению с M54, удельную мощность удалось снизить с 1,0 кг/кВт до 0,82 кг/кВт.
Новаторские решения
Благодаря последовательному внедрению облегченных конструкций масса двигателя N52 стала на 10 кг меньше, чем у его предшественника M54. Этому в большой степени способствовало использование магниево алюминиевого блок картера и облегченного выпускного коллектора. Особую роль в этом сыграло использование магния в таких деталях, как, например, нижняя часть блок картера (Bedplate) и крышка головки блока цилиндров. Благодаря этим мерам прежде всего была существенно снижена удельная масса, что в конечном итоге отразилось и на расходе топлива.

Компоненты двигателя BMW N52
В двигателе N52 использованы некоторые новаторские решения, которые помогают еще более усовершенствовать силовой агрегат в целом. К ним относятся:
- магниево алюминиевый блок картер;
- инновационная система газообмена VALVETRONIC II;
- масляный насос с регулируемым объемным расходом;
- электрический насос охлаждающей жидкости;
- трехступенчатая раздельная система всасывания;
- крышка головки блока цилиндров из магниевого сплава;
- переход на одноременный привод;
- термостойкий коллектор облегченной конструкции (с герметичными соединениями – LSI);
Компоненты базового двигателя
- шестицилиндровый рядный двигатель с 4 мя клапанами на цилиндр;
- уменьшение трения благодаря изменению размера подшипников и снижению сопротивления при эксплуатации;
- блок картер из сплава магния и алюминия из двух частей;
- шатун трапециевидной формы;
- головка блока цилиндров из кремниево алюминиевого сплава (Alusil);
- блок ГРМ встроен в блок картер и в головку блока цилиндров;
- уплотнительная прокладка головки блока цилиндров с силиконовым уплотнением;
VALVETRONIC II- оптимизированный по массе двойной VANOS;
- привод клапанов с изменяемым ходом 2;
- управление встроено в электронную систему управления двигателем;
- масляный насос с регулируемым объемным расходом;
- электрический насос охлаждающей жидкости;
- вентиляция картера со встроенным обогревом;
- трехступенчатая раздельная система всасывания;
Магний – новый материал в двигателестроении
Поскольку возможности снижения веса за счет использования алюминиевых картеров уже исчерпаны, необходимо начать переход к использованию магния.

Динамика изменения массы картера рядных двигателей:
A – Масса картера (in %); 1 – Серый чугун, литье в песчаные формы; 2 – Alusil (функциональная интеграция для P>55 кВт/л, литье под низким давлением); 3 – Mg/Al (функциональная интеграция для P>55 кВт/л двухслойное литье);
Выдающимся свойством магния и его сплавов является его малая плотность, равная прибл. 1,8 г/куб.см.
Высокие литьевые свойства определенных сплавов магния позволяют изготавливать большие по площади и сложные по форме литые детали с высоким качеством поверхности. За счет низкой температуры плавления, малой энергии плавления и теплоемкости в пересчете на объем магния при литье можно получить повышение прочности до 50 % по сравнению с деталями из литого алюминия.
Несмотря на высокую точность литых деталей, все же почти неизбежно возникает необходимость в заключительной обработке функциональных поверхностей (резанием). При этом раскрывается еще одно преимущество магния – его исключительная податливость резанию.
Эти отличные качества легко опровергают точку зрения, согласно которой использование магния и его сплавов является проблематичным.
Проблемы коррозии, которые ранее стояли весьма остро, потеряли свою актуальность благодаря созданию устойчивых к коррозии сплавов. Сплав, применяемый для двигателя N52, называется AJ62.
Тем не менее, может возникнуть явная угроза коррозии, если не соблюдать приводимые далее правила, касающиеся конкретных материалов.
Не допускается использование неаттестованных материалов для деталей, которые вступают в контакт с магниевыми деталями.
Это значит, что следует устанавливать только оригинальные запасные части BMW. Материал навесного агрегата должен либо сочетаться со сплавом AJ62, либо его нужно изолировать от магниевого картера.

Изоляция электрического насоса охлаждающей жидкости
Конструктивное использование магния
Поскольку магний нельзя использовать в определенных местах, например, на рабочих поверхностях цилиндров, то блок цилиндров изготавливается в виде составной конструкции.

Блок цилиндров N52 из магниево алюминиевого сплава:
1 – Верхняя часть блока цилиндров; 2 – Нижняя часть блока цилиндров;
Блок цилиндров состоит из алюминиево кремниевой вставки, которая окружена магниевым сплавом и составляет с ним единую деталь. Магниевый сплав AJ62 разработан инженерами концерна BMW.

Магниево алюминиевый блок цилиндров Н52 в разрезе:
1 – Магниево алюминиевый блок цилиндров; 2 – Алюминиево кремниевая вставка;
Алюминиево кремниевая вставка используется для того, чтобы болты крепления коробки передач, головка блока цилиндров, подшипник коленвала и каналы охлаждения, а также охлаждающая жидкость и содержащаяся в ней вода не вступали в контакт с магнием.
Блок цилиндров можно подвергать шлифованию.
Нижняя часть блока цилиндров

Разъемный магниево алюминиевый блок цилиндров N52:
1 – Вставки в нижней части блока цилиндров; 2 – Нижняя часть блока цилиндров;
В двигателе N52 применяется разъемный блок цилиндров, уже известный по четырехцилиндровым двигателям.

Нижняя часть блока цилиндров Н52 из сплава AJ62 со стальными вставками:
При монтажных работах и при работах по герметизации применяется та же технология, что и для N42.
Электрохимические свойства магния
Металлы делятся на благородные и неблагородные. Например, золото является благородным металлом, а натрий – очень неблагородным. Остальные металлы занимаю места между ними. Когда контактирующие между собой металлы, такие как железо и магний, погружаются в электропроводящую жидкость, например, в солевой раствор, то неблагородный металл растворяется в нем. Кроме того, от благородного металла к неблагородному протекает электрический ток. Неблагородный металл при этом оседает на благородном металле.
Магний является неблагородным металлом. Поэтому его поверхность легко разъедается другими веществами. Но магниевый сплав, используемый в N52, ведет себя совершенно по другому. При добавлении другого металла негативные свойства чистого металла исчезают, и это обеспечивает соблюдение всех предъявляемых к нему требований.

Электрохимическая коррозия железа и магния
Между обоими металлами, находящимися в электролите, возникает электрический потенциал. Все металлы можно классифицировать в соответствии с этим потенциалом. Железо в этом ряду классификации занимает среднее положение, а алюминий и особенно магний являются неблагородными. Электрохимическая коррозия идет тем быстрее, чем большей является разность потенциала между металлами.
Описанная выше лабораторная реакция происходит и в двигателе, когда два металла непосредственно контактируют между собой, а контактная поверхность смочена, например, брызгами воды. Возникает так называемая контактная коррозия. Она еще более усиливается, если между контактными поверхностями имеется зазор, в который попадает влага. алюминием и сталью не создают никаких проблем.
Контактной коррозии можно избежать, если поддерживать контактные поверхности сухими или покрыть их моторным маслом, не проводящим электрическийток. Поэтому внутри двигателя все контактные поверхности между магнием, алюминием и сталью не создают никаких проблем.
Физические свойства материалов
Магний и алюминий обладают почти одинаковым коэффициентом расширения, который, однако, почти вдвое больше, чем у стали:
- магний: 0,0026 % на °C
- алюминий: 0,0023 % на °C
- сталь: 0,0011 % на °C
Температура плавления магния почти не отличается от температуры плавления алюминия. Тогда как температура плавления стали существенно выше:
- магний: 650 °C
- алюминий: 660 °C
- сталь: 1750 °C
Электрическая проводимость алюминия и магния существенно выше, чем у стали. Поэтому эти материалы хорошо подходят для экранирования электромагнитных помех (например, от работы системы зажигания).
Одинаковый коэффициент расширения алюминия и магния обеспечивает беспроблемное соединение обоих металлов. Поскольку коэффициент расширения стали в два раза меньше, в двигателе N52 нельзя использовать стальные болты. При нагревании двигателя стальной болт расширяется в два раза меньше, чем блок цилиндров. И наоборот, при охлаждении существует опасность того, что резьбовое соединение из стали будет зажато. Поэтому в ответственных местах устанавливаются алюминиевые болты.
Обработка магния резанием
Работы с этим материалом, часто выполняемые на СТО, не рассматриваются как опасные. Поскольку образуется малое количество стружки (например, при калибровке резьбы), не требуется устройства специальной вытяжки.
Тем не менее, при большом объеме работ с магниево алюминиевыми блоками цилиндров необходимо предотвратить скапливание взрывоопасного водорода в контейнере для стружки, а также удалять оттуда влагу. Под влагой здесь подразумевается только вода или водосодержащие соединения.
Правила при обработки резанием
Несмотря на то, что детали из магниевых сплавов хорошо поддаются сухой обработке резанием, последним словом техники является их “мокрая” обработка. При этом используется масло для смазки и охлаждения режущего инструмента или эмульсия. При обработке резанием самую большую опасность представляет стружка. Особенно опасна влажная стружка, но стружка, смоченная маслом, устойчива к возгоранию, и поэтому в процессе обработки с маслом она не может
воспламениться.
Магний и вода могут вступать между собой в реакцию с образованием гидроксида магния и водорода. Поэтому при обработке с использованием эмульсии возникает опасность взрыва водорода, если постоянно выделяющийся водород будет скапливаться и его концентрация станет критической. Поэтому следует предусмотреть удаление влаги из контейнера для стружки.
Помимо этого, следует немедленно удалять стружку из эмульсии, поскольку быстро наступает омыление или повышение вязкости эмульсии, и она становится непригодной к использованию.
При обработке магния можно использовать тот же ряд режущих материалов, что и при обработке алюминия, то есть быстрорежущую сталь, твердые сплавы и поликристаллические алмазы (PKD).
Шлифование требует особого внимания
Шлифование с влажным охлаждением следует рассматривать с другой точки зрения, чем прочие виды обработки резанием. Дело в том, что при шлифовании образуется тончайшая стружка (шлифовальная пыль), которая в определенной пропорции с воздухом взрывается при случайном воспламенении (например, от искр из дымохода, искрения при сварке). Для частиц магния диаметром прибл. 50 мкм огнеопасная концентрация составляет 15–30 г/м 3 . Если обработка с охлаждением невозможна или слишком хлопотна, то образующуюся при шлифовании пыль следует удалять и осаждать ее в отстойнике с водой.
Работы с магнием, связанные с образованием пыли, следует выполнять только при наличии подходящей вытяжки.
Важным показателем опасности магния является удельная поверхность изделия, то есть соотношение между поверхностью и объемом. С точки зрения техники безопасности сплошные детали не представляют собой опасности. Даже при сильном воздействии тепла они практически не воспламеняются.
Напротив, стружка и пыль легко вступают в реакцию. Критическая температура, при которой сухая и тонкая стружка может воспламениться, составляет 450-500 °C. Неправильная геометрия резания или использование затупившегося инструмента при сухой обработке могут стать причиной такого нагрева. Другим источником опасности могут стать искровой разряд при соприкосновении инструментов или обработка стали. Если же, несмотря на все меры предосторожности, произошло возгорание магния, для его тушения ни в коем случае нельзя использовать воду или водосодержащее средство пожаротушения (образование водорода, взрыв гремучего газа!). Нельзя также применять порошковые огнетушители, двуокись углерода и азот.
Уплотнения
Контактной коррозии можно избежать, если проложить между металлами уплотнение, не проводящее электрический ток. В данном случае речь идет об уплотнительных прокладках масляного картера и головки блока цилиндров, которые отделяют масляный картер и головку блока, изготовленные из алюминия, от блока цилиндров, изготовленного из магния.

Выступающая за край уплотнительная прокладка масляного картера N52
Ситуация с уплотнительной прокладкой головки блока цилиндров аналогична. Тем не менее, следует обратить внимание на то, чтобы уплотнительная прокладка головки блока цилиндров двигателя N52, в отличие от прежних прокладок, была снабжена рабочей кромкой уплотнения. Такая кромка препятствует образованию своеобразной перемычки из грязи и брызг воды и, тем самым контакту между металлами.
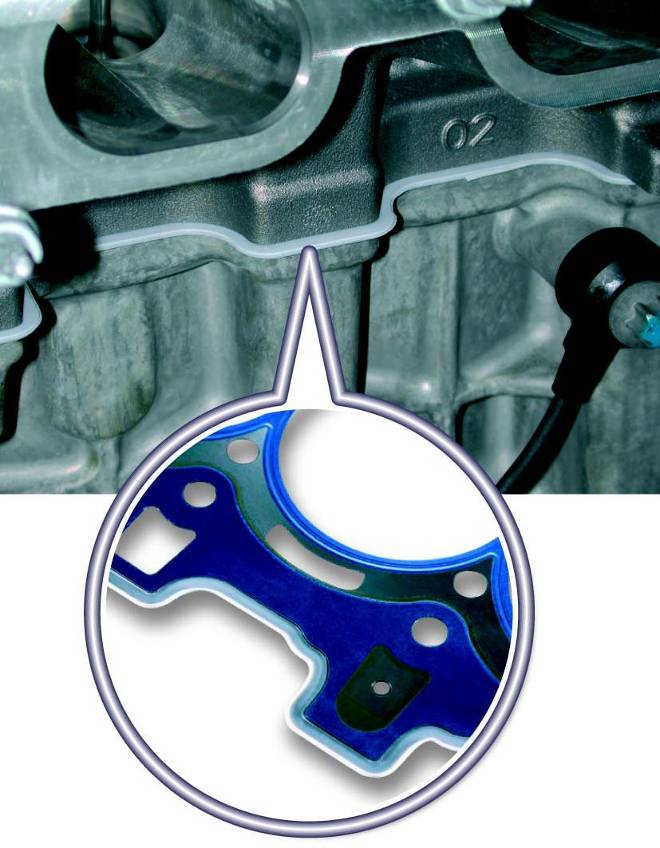
Рабочая кромка уплотнительной прокладки головки блока цилиндров N52
Указанные уплотнительные прокладки нельзя повреждать, например, при установке навесного оборудования. При повреждении уплотнительной прокладки в течение весьма непродолжительного времени возникает контактная коррозия между алюминием головки блока цилиндров и магнием блока цилиндров. При глубоких повреждениях рабочей кромки уплотнения может сыграть отрицательную роль сталь, находящаяся в сердцевине прокладки, поэтому поврежденные уплотнительные прокладки следует заменять.
Резьбовые соединения
Резьбовые соединения двигателя требуют особого внимания. При выворачивании болтов следует немедленно просушить резьбовые отверстия струей сжатого воздуха, чтобы предотвратить их коррозию при контакте с охлаждающей жидкостью.

Продувка резьбовых отверстий сжатым воздухом в Н52
Само собой разумеется, что перед заворачиванием болтов резьбовые отверстия должны быть абсолютно сухими, чтобы впоследствии в них не возникла контактная коррозия между материалом блока цилиндров и болтом.
Поскольку коэффициенты расширения материалов различны, на всех резьбовых соединениях на N52, которые выполнены из магния, используются не стальные, а алюминиевые болты. Крышка головки блока цилиндров (из магния) также крепится к алюминиевой головке блока цилиндров алюминиевыми болтами.

Головка алюминиевых болтов в Н52 окрашена в синий цвет
Ввиду того, что алюминий обладает малым пределом прочности при растяжении по сравнению со сталью, алюминиевые болты следует затягивать в точном соответствии с установленным порядком.

Порядок затяжки алюминиевого болта в N52:
(I) – Момент затяжки; (II) – Угол затяжки;
Прежде всего следует затянуть болт, прилагая определенный момент затяжки (I). Этот момент выбран с таким расчетом, чтобы между соединяемыми деталями был полностью выбран зазор, но при этом сам болт еще не был бы нагружен. Наконец, следует довернуть болт на определенный угол (II). При этом достигается требуемое натяжение болта.
Алюминиевые болты следует использовать только один раз, и поэтому после каждого выворачивания их необходимо заменять.
Система газообмена VALVETRONIC II

Головка блока цилиндров двигателя N52 в разрезе
С выпуском N52 рядный шестицилиндровый бензиновый двигатель получил систему управления нагрузкой посредством привода клапанов. Уже VALVETRONIC I, который использовался в четырех , восьми и двенадцатицилиндровых двигателях, позволил значительно увеличить коэффициент полезного действия.
В продолжение развития этой концепции концерн BMW выпустил систему VALVETRONIC II.
Результатом дальнейшего развития явились:
- повышение динамических показателей двигателя;
- повышение эффективности;
- улучшение показателей выброса ОГ;
Эти результаты еще ярче подчеркивают качества, присущие автомобилям BMW. Вождение машины с двигателем, на котором были произведены такие изменения, доставляет еще большее удовольствие:
- Максимальная частота вращения повысилась до 7000 об/мин;
- Литровая мощность повысилась на 63,4 кВт/л;
- Удельный крутящий момент двигателя в широком диапазоне частоты вращения составляет прибл. 100 Нм/л;
- Значительный рост ускорения клапанов и снижение трения передающих деталей обеспечивают улучшение параметров реагирования;
- Уменьшение выброса CO 2 более чем на 10 % в NEFZ (Новый Европейский Цикл Движения);
- Соблюдены самые строгие требования по токсичности ОГ;
Управление нагрузкой

Нагрузка на двигатель – слева с дроссельной заслонкой – справа с VALVETRONIC:
OT – Верхняя мертвая точка; UT – Нижняя мертвая точка; 1 – Впускные клапаны открываются; 2 – Выпускные клапаны закрываются; 3 – Впускные клапаны закрываются; 4 – Выпускные клапаны открываются; 5 – Момент зажигания; A – Полезная работа; B – Потеря работы; P – Давление;
На левом рисунке представлен традиционный способ работы с относительно высокими потерями. На правом рисунке легко проследить снижение потерь. Верхняя зона представляет собой полезную мощность, отдаваемую бензиновым двигателем в процессе сгорания топлива. Нижняя зона наглядно демонстрирует потери при этом процессе.
Площадь потерь может быть приравнена к работе по газораспределению. При этом речь идет об энергии, которая должна быть затрачена на то, чтобы вытолкнуть отработавшие газы из цилиндра и затем всосать в цилиндр свежую бензо-воздушную смесь. Всасывание свежей смеси в двигателе, управляемом при помощи дроссельной заслонки, за исключением положения полной нагрузки, всегда проходит при сопротивлении дроссельной заслонки, которая располагается на пути воздушного потока. В процессе всасывания двигателя с VALVETRONIC дроссельная заслонка почти всегда полностью открыта. Управление нагрузкой осуществляется путем изменения времени закрытия клапанов.
В отличие от традиционного двигателя, управляемого при помощи дроссельной заслонки, во впускном коллекторе разрежение не создается. Это значит, что энергия на создание разрежения не затрачивается. Более высокий КПД достигается благодаря снижению потерь в процессе всасывания.
Для вентиляции картера требуется минимальное разрежение во впускном коллекторе. Для этого дроссельная заслонка слегка закрывается.
Устройство/принцип работы
VALVETRONIC II состоит из узла управления ходом клапанов, объединенного с системой газораспределения с изменяемой фазой открытия впускных клапанов (двойной VANOS). Выполняется управление ходом только впускных клапанов, тогда как а регулировка углового положения выполняется для обоих распределительных валов.
Управление нагрузкой без помощи дроссельной заслонки осуществляется за счет:
- изменения хода впускного клапана;
- изменения времени открытия впускного клапана;
- изменения фазы газораспределения распредвалов впускных и выпускных клапанов;
По принципу управления нагрузкой система VALVETRONIC II соответствует системе VALVETRONIC I, применяемой в двигателе N42.
Оптимизация системы достигается за счет изменения кинематики привода клапанов, изменения в серводвигателе и скорректированных фаз газораспределения узлов VANOS.
Основные различия:
- на промежуточном рычаге вместо подшипника скольжения эксцентрикового вала установлен роликовый подшипник. Благодаря этому уменьшается трение в приводе клапанов;
- ход промежуточного рычага стал точнее. Необходим только пружинный фиксатор для обеспечения хода и крепления промежуточного рычага;
- подвижная масса привода клапанов уменьшилась на 13 %;
- длину хода впускного клапана удалось значительно увеличить. Максимальный ход клапана увеличен до 9,9 мм, но прежде всего удалось уменьшить минимальный ход до 0,18 мм;
К этому добавляется улучшения динамики всасывания и выпуска.

Работа VALVETRONIC на взаимодействии диапазона регулировки VANOS:
OT – Верхняя мертвая точка; UT – Нижняя мертвая точка; 1 – Впускные клапаны открываются; 2 – Выпускные клапаны закрываются; 3 – Впускные клапаны закрываются; 4 – Выпускные клапаны открываются; 5 – Момент зажигания; A – Диапазон регулировки VANOS; B – Диапазон регулировки привода клапанов с изменяемым ходом; P – Давление;
Привод клапанов с изменяемым ходом II в Н52
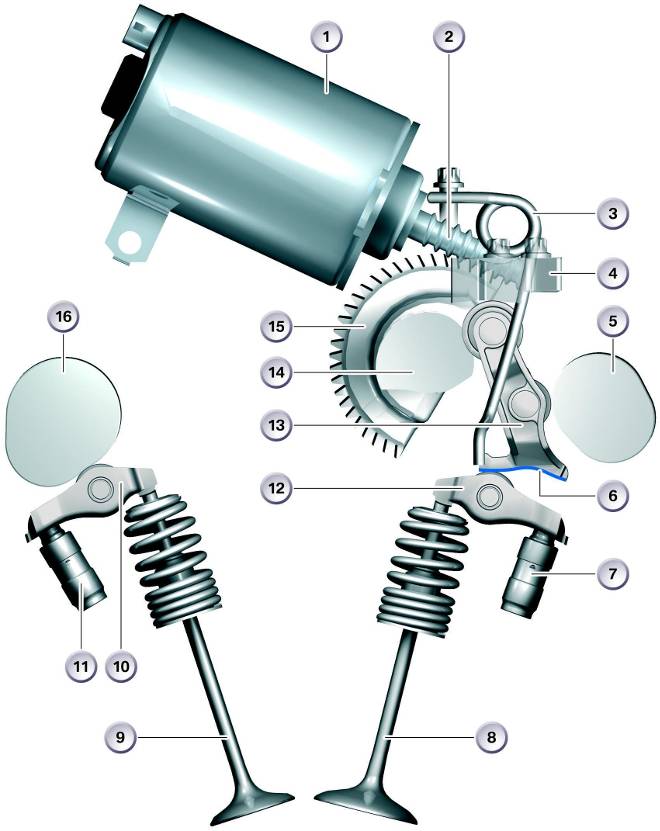
Управление клапанами с изменяемым ходом II в Н52:
1 – Серводвигатель; 2 – Червячный вал; 3 – Возвратная пружина; 4 – Кулисный блок; 5 – Распредвал впускных клапанов; 6 – Рампа; 7 – Гидравлическая система компенсации клапанного зазора (HVA) на стороне впуска; 8 – Впускной клапан; 9 – Выпускной клапан; 10 – Роликовый рычаг толкателя на стороне выпуска; 11 – Гидравлическая система компенсации клапанного зазора (HVA) на стороне выпуска; 12 – Роликовый рычаг толкателя на стороне впуска; 13 – Промежуточный рычаг; 14 – Эксцентриковый вал; 15 – Червячное колесо; 16 – Распредвал выпускных клапанов;
Управление клапанами с изменяемым ходом осуществляется при помощи серводвигателя (1), эксцентрикового вала (14), промежуточного рычага (13), возвратной пружины (3), распредвала (5) впускных клапанов и роликового рычага (12) толкателя.

Минимальный ход клапана в БМВ Н52
Серводвигатель установлен над распределительным валом на головке блока цилиндров. Он служит для регулировки положения эксцентрикового вала. Червячный вал электродвигателя захватывает червячное колесо эксцентрикового вала.
После регулировки нет необходимости слишком сильно блокировать эксцентриковый вал, поскольку червячная передача обладает достаточным самоторможением. Эксцентриковый вал регулирует ход впускных клапанов.

Максимальный ход клапана в Н52
Промежуточный рычаг изменяет передаточное число между распределительным валом и роликовым рычагом толкателя. В положении полной нагрузки ход клапана (9,9 мм) и продолжительность открывания максимальны. В положении холостого хода ход клапана (0,18 мм) и продолжительность открывания минимальны.
Роликовый рычаг толкателя и соответствующий промежуточный рычаг подразделяются на четыре класса. На детали выбит соответствующий код. Каждая пара всегда относится к одному классу. Благодаря взаимному соотнесению при изготовлении роликового рычага толкателя и промежуточного рычага удалось достичь того, что даже при минимальном ходе, составляющем 0,18 мм, цилиндр заполняется равномерно.
Датчик эксцентрикового вала

Датчик VALVETRONIC и колесико на эксцентриковом валу в N52:
1 – Магнитное колесико; 2 – Болт крепления (немагнитный); 3 – Датчик эксцентрикового вала;
Датчик (3) эксцентрикового вала передает сигнал о положении вала в DME. Его работа основана на магниторезистивном принципе: ферромагнитный проводник изменяет свое сопротивление, когда вокруг него изменяется магнитное поле. Для этого на эксцентриковом валу установлено магнитное колесико (1), в котором расположен постоянный магнит. Силовые линии магнитного поля этого магнита при вращении вала пересекают магнитопроводящий материал в датчике. Получающееся таким образом изменение сопротивления служит регулируемой величиной для сигнала блока управления двигателем.
Магнитное колесико должно быть закреплено на эксцентриковом валу немагнитным винтом (2), иначе датчик не будет работать.
Крайние положения MIN/MAX

Упор MIN эксцентрикового вала в Н52:
1 – Упор MIN на эксцентриковом валу; 2 – Упор MIN вверн. в головку блока цилиндров;

Упор MAX эксцентрикового вала в Н52
Для распознавания механических упоров можно выполнить специальную процедуру, в ходе которой эксцентриковый вал будет перемещаться от нулевого хода до полного хода. Процедура распознавания упоров выполняется только тогда, когда при запуске блок управления двигателем выдает неправдоподобные значения. Она может быть также запущена диагностической системой.
Фазировка
Привод клапанов с изменяемым ходом и VALVETRONIC II выполняют очень быстрое и точное управление двигателем.
В нижнем диапазоне хода клапана возможность настройки поддерживается за счет так называемой фазировки. При этом впускные клапаны цилиндра синхронно открываются на 0,2 мм. Начиная с этого хода, клапан 1 начинает опережать остальные. Клапан 2 открывается с незначительной задержкой и догоняет клапан 1 прибл. на ходе 6 мм. Начиная с этого момента, они открываются синхронно.
Такое соотношение при открывании благоприятствует поступлению смеси в цилиндры. Благодаря малому проход ному сечению впускного клапана при равномерном всасывании объема обеспечивается более высокая скорость потока. Такая скорость потока в сочетании с геометрией верхней части камеры сгорания обеспечивает лучшее перемешивание всасываемой смеси.
VANOS

Двойная система VANOS двигателя N52
N52 снабжен компактными бесступенчатыми лопастными исполнительными узлами VANOS на стороне впуска и выпуска. Системы VANOS легко снимаются и устанавливаются. Они выполнены в виде встроенной составной части цепного привода и крепятся центральным болтом на распределительном валу.

Спиральная пружина удерживает VANOS в исходном положении
Регулировка фаз газораспределения осуществляется так же, как и на N42. При отсутствии давления система VANOS удерживается в исходном положении за счет витой пружины.
Следует строго соблюдать руководство по ремонту. Узел VANOS теперь является неразборным. Поскольку узлы VANOS на стороне выпуска и впуска имеют различные фазы газораспределения, их нельзя менять местами. Неправильная установка узлов VANOS приведет к серьезному повреждению двигателя.

Исполнительный узел VANOS на стороне впуска
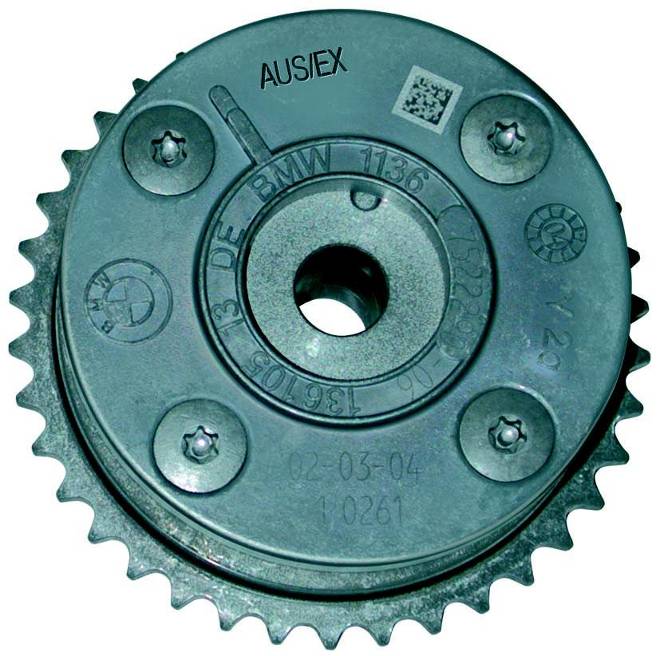
Исполнительный узел VANOS на стороне выпуска
Масляный насос с регулированием расхода по объему
Система смазки и, прежде всего, масляный насос подчинены требованиям, предъявляемым к системе двигателя в целом:
- увеличение мощности;
- уменьшение массы;
- оптимизация расхода топлива;
- снижение вредных выбросов;
Масляный насос отнимает значительную часть общей мощности двигателя, расходуемую на навесное оборудование.
Этот потенциал экономии положен в основу оптимизации системы насоса.
Масло служит для:
- смазки трущихся поверхностей двигателя;
- охлаждения высоконагруженных частей;
- отвода продуктов истирания;
- привода в качестве гидравлической жидкости;
- защиты от коррозии;
Особенно большое количество масла необходимо узлам VANOS в момент регулировки углов положения распредвалов. Но для поддержания угла распредвалов VANOS больше не нуждается в потоке масла. Поэтому потребность в масле взаимосвязана с масштабом регулировки.
Обычные масляные насосы создают такое давление, при котором создается максимальный поток масла в двигателе.
Во многих рабочих режимах это приводит к бесполезному расходу энергии в масляном насосе и к избыточному износу масла.
Новая оптимизированная система насоса основывается на VALVETRONIC II и на так называемом “горячем” холостом ходе, т. е. при работе двигателя с высокой температурой масла и на малых оборотах.
Наибольшую потребность в регулировке VANOS возникает в режиме холостого хода при малом ходе клапанов. В этом рабочем диапазоне потребность в корректировке начала открывания клапанов (точное управление двигателем) пропорционально возрастает до максимума.
Это заставляет масляный насос при относительно малых оборотах подавать большой объем масла на узлы VANOS.
Для того чтобы удовлетворять таким требованиям, обычный масляный насос должен быть в три раза большим по раз меру, чем насос, используемый в N52. Соответственно, он бы забирал больше энергии привода.
В N52 установлен масляный насос с регулированием объема. Насос этого типа подает только то количество масла, которое требуется двигателю в данном рабочем режиме. В режимах с малой нагрузкой не будет подаваться излишнее количество масла. Это снижает расход топлива и продлевает срок службы масла.
В качестве насоса используется маятниковый шиберный насос. Вал насоса установлен в корпусе устройства подачи эксцентрично, а лопасти при вращении перемещаются радиально. За счет этого лопасти образуют камеры различных объемов. При возрастающем объеме масло всасывается, а при уменьшающемся объеме – выталкивается в масляные каналы.

Масляный насос БМВ Н52:
1 – Лопасти; 2 – Маятниковый шибер; 3 – Маятниковое крепление регулирующего поршня; 4 – Пружина сжатия; 5 – Вал насоса; 6 – Ротор; 7 – Ось вращения;
Преимущества масляного насоса с регулированием расхода по объему
- благоприятное соотношение конструктивного объема/коэффициента полез ного действия;
- создание гидравлической мощности в соответствии с потребностями; используется меньше мощности двигателя, вследствие чего повышается коэффициент полезного действия;
- небольшие колебания объема потока;
- минимально возможное вспенивание масла в самой системе подачи;
- гидравлическая энергия не преобразуется в потери тепла;
- предотвращение преждевременного старения масла;
- низкий шум при работе;
- высокая динамика регулирования (скачки давления отсутствуют даже при пуске холодного двигателя);
- устойчивость к загрязнению;
Принцип работы масляного насоса с регулируемым расходом по объему
Насос приводится в действие от коленчатого вала через цепь. Создаваемое давление масла воздействует на регулирующий поршень с косыми опорными поверхностями (маятниковое крепление) против силы пружины сжатия. Маятниковое крепление изменяет положение маятникового шибера. Если вал насоса находится по центру шибера, то изменения объема становятся малыми, а производительность насоса – невысокой. Если вал насоса располагается не по центру, то изменения объема и производительность насоса возрастают.
При повышении потребности в масле, например, при регулировке VANOS, давление в системе смазки падает и, следовательно, падает давление на регулирующий поршень. Насос увеличивает объем подачи и восстанавливает прежнее значение давления. При восстановлении потребности двигателя в масле насос соответственно уменьшает производительность в направлении подачи 0.

Регулирующий поршень с маятниковым креплением:
Электронный контроль состояния масла
На двигателях N52 маслоизмерительный щуп с направляющей трубкой отсутствует. Это создает удобства для владельца. Благодаря этому обеспечивается более точное определение состояния масла.
Уровень масла в двигателе измеряется датчиком состояния масла (ÖZS) и передается на центральный информационный дисплей (CID) в E63. Температура и уровень масла в двигателе также измеряются и вычисляются датчиком ÖZS. Сигнал с ÖZS обрабатывается в DME. Далее обработанный сигнал передается через PT CAN, модуль безопасности и межсетевого обмена (SGM) и K CAN на комбинацию приборов и на CID.
Измерение уровня масла предотвращает его недопустимое падение и, тем самым, повреждение двигателя. Отслеживание состояния масла позволяет точно определить, когда требуется его замена. При переполнении двигателя, которое может привести к его негерметичности, высвечивается предупреждение.
Датчик состояния масла (ÖZS)

Датчик состояния масла двигателя БМВ Н52:
1 – Корпус; 2 – Наружная металлическая трубка; 3 – Внутренняя металлическая трубка; 4 – Моторное масло; 5 – Датчик уровня масла; 6 – Датчик состояния масла; 7 – Электронный блок датчика; 8 – Масляный картер; 9 – Датчик температуры;
Принцип работы датчика состояния масла
Датчик состоит из двух цилиндрических конденсаторов, расположенных один над другим.
Определение состояния масла производится посредством нижнего малого конденсатора (6).
В качестве электродов конденсатора используются две металлические трубки (2 + 3), вставленные одна в другую. Между электродами находится диэлектрик – моторное масло (4). Электрические свойства моторного масла изменяются по мере его старения и истощения топливных присадок.
Диэлектрик: токонепроводящее вещество в электрическом поле. Электрическое поле проходит через диэлектрик. При изменении электрических свойств моторного масла (диэлектрика) изменяется емкость конденсатора (датчика состояния масла). Это значение емкости преобразуется встроенным в датчик электронным блоком (7) в цифровой сигнал. Цифровой сигнал передается в DME в качестве информации о состоянии масла в двигателе. DME использует это фактическое значение в качестве основы для расчета времени следующей замены масла. Уровень масла в двигателе измеряется в верхней части датчика (5). Эта часть находится в масляном картере на уровне масла. При падении уровня масла (диэлектрика) соответствующим образом изменяется емкость конденсатора. Электронная схема датчика преобразует значение емкости в цифровой сигнал, который посылается на блок DME. Возможные неисправности/последствия Электронный блок датчика состояния масла снабжен функцией самодиагностики. При неисправности ÖZS в DME передается сообщение о неисправности. Для измерения температуры масла в двигателе используется платиновый датчик температуры (9), расположенный у основания датчика состояния масла. Отслеживание уровня масла в двигателе, его температуры и состояния осуществляется непрерывно в течение всего времени, когда на контакт 15 подается напряжение. Подача напряжения питания на датчик состояния масла осуществляется с контакта 87.
Возможные неисправности/последствия
Электронный блок датчика состояния масла снабжен функцией самодиагностики.
При неисправности ÖZS в DME передается сообщение о неисправности.
Электронный контроль уровня масла
Измерение уровня масла осуществляется в два этапа:
статическое измерение уровня масла на стоящем автомобиле;
динамическое измерение уровня масла во время движения;
Статическое измерение уровня масла при выключенном двигателе
Это только приблизительное измерение, т. к. ÖZS при выключенном двигателе распознает только минимальный уровень масла. Уровень масла правильно измеряется только на работающем двигателе!
При статическом измерении уровня масла водитель может при включенном зажигании определить, достаточен ли уровень масла для уверенного пуска двигателя.
- Важно, чтобы автомобиль стоял в горизонтальном положении, иначе результат измерения будет неправильным.
- Выберите функцию бортового компьютера “Service” (ТО) > “Ölstand” (Уровень масла).
Если для уверенного пуска двигателя имеется достаточное количество масла, на CID появляется графическое изображение двигателя с зеленым маслосборником.

Контроль уровня масла 1
Если уровень наполнения близок к минимуму, появляется пиктограмма с желтым маслосборником и маслоизмерительным щупом, которое желтым цветом обозначает низкий уровень наполнения.
Необходимость в доливе масла +1 литр также отображается в виде текстового сообщения.
При доливе менее 1 литра индикация не изменяется. Только при доливе 1 литра будет показан максимальный уровень.

Контроль уровня масла 2
Если уровень наполнения находится ниже минимума, появляется графическое изображение красного маслосборника и маслоизмерительного щупа, которое красным цветом обозначает низкий
уровень наполнения.
Необходимость в доливе масла +1 литр также отображается в виде текстового сообщения.
При доливе менее 1 литра индикация не изменяется. Только при доливе 1 литра будет показан максимальный уровень.

Контроль уровня масла 3
Если уровень наполнения выше максимума, появляется графическое изображение с желтым маслосборником и маслоизмерительным щупом, которое желтым цветом обозначает высокий уровень наполнения.
Об этом водителя также известит текстовое сообщение.

Контроль уровня масла 4
Динамическое измерение уровня масла во время движения
После замены масла всегда следует производить динамическое измерение уровня масла (в течение прибл. 5 минут движения). Поскольку после замены масла отображается последняя записанная величина уровня масла, это может привести к ошибочной интерпретации уровня масла. При замене или перепрограммировании блока управления двигателем последняя величина уровня масла не записывается, и поэтому на дисплей будет выведено сообщение "Уровень масла ниже мин.". Только приблизительно через 5 минут работы двигателя будет отображен правильный уровень масла.
- Запустите двигатель.
- Выберите функцию бортового компьютера “Ölstand prüfen” (Проверить уровень масла).
- Уровень масла измеряется. В ходе измерения может появиться символ часов. Символ часов может отображаться до 50 секунд после пуска двигателя, если нет результата измерения, или если результат длительного измерения не попадает в допустимый диапазон только что измеренного уровня масла.
Динамическое измерение уровня масла начинается, когда достигаются следующие параметры:
- температура двигателя > 60 °C;
- частота вращения коленвала двигателя > 1000 об/мин;
- поперечное и продольное ускорение < 4 5 м/с(2). Поступил сигнал поперечного ускорения от DSC. На автомобилях без DSC учитывается только продольное ускорение, которое рассчитывается на основе факторов скорости и времени;
- уклон < 5 % на протяжении 200 м движения по наклонному участку пути. Величина уклона определяется при помощи датчика давления окружающей среды в DME. По достижении этих параметров показание уровня масла обновляется. После этого уровень масла измеряется непрерывно, а показание обновляется каждые 20 минут. При динамическом измерении уровня масла во время движения через 15 с после показания уровня масла происходит выход из меню “Ölstand prüfen” (Проверить уровень масла) (скорость движения > 0);
Возможные индикации
Уровень масла в пределах нормы при выключенном двигателе
- на CID появляется графическое отображение уровня масла и указание O. K., что свидетельствует о том, что уровень масла достаточен для работы двигателя;

Контроль уровня масла 5
Уровень масла в пределах нормы при холостом ходе
- на CID появляется графическое отображение уровня масла и указание O. K., что свидетельствует о том, что уровень масла достаточен для работы двигателя;
- далее появляется еще одно графическое изображение, представляющее собой маслоизмерительный щуп;
- Оно показывает уровень масла зеленым цветом;
- Контроль уровня масла 6
- Контроль уровня масла 7
Недостаточный уровень масла
- на CID появляется графическое отображение уровня масла и сообщение о необходимости долить 1 литр масла. Если не долить масло, это требование будет повторяться снова и снова до тех пор, пока не будет превышен минимальный уровень масла;
Уровень масла слишком высок
- на CID появляется графическое отображение уровня масла и сообщение о том, что максимальный уровень масла превышен. Избыточное количество моторного масла следует откачать до максимальной границы на СТО. Пока не будет откачано избыточное количество масла, это требование будет повторяться снова и снова до тех пор, пока уровень масла не опустится до максимального. Таким преимуществом обладает система контроля, дружественная по отношению к пользователю. При переполнении двигателя маслом (угроза его разгерметизации) на комбинацию приборов выводится предупреждение;
ТО
Если на дисплее появилось сообщение “SERVICE” (ТО), это свидетельствует о неисправности системы измерения. В этом случае уровень масла прогнозируется на основе последней измеренной величины расхода масла. Он отображается на дисплее. Нет необходимости срочно обращаться на СТО. В меню “Service” показывается остаточный пробег. При неисправности комбинации приборов уровень масла можно также считать при помощи диагностического тестера.
Система охлаждения
С охлаждающим контуром складывается такая же ситуация, что и с масляным. На предыдущих двигателях производительность насоса охлаждающей жидкости устанавливалась в соответствии с максимальными потребностями двигателя в охлаждении, но сейчас такая необходимость в большинстве случаев отпадает. Поэтому через термостат по малому контуру циркулирует по большей части неиспользуемое избыточное количество охлаждающей жидкости. В области охлаждения также была осуществлена оптимизация системы, что позволило снизить мощность потерь.
Благодаря этому новая система обеспечивает температурный режим, согласованный с нагрузкой двигателя.
Насос охлаждающей жидкости с электронным управлением

Электрический насос охлаждающей жидкости с жидкостным охлаждением:
1 – Насос; 2 – Двигатель; 3 – Микросхема (EWPU);
Насос охлаждающей жидкости на N52 представляет собой центробежный насос с электроприводом. Мощность электродвигателя регулируется электронной микросхемой (EWPU), которая находится под соединительной крышкой двигателя.
EWPU связан с блоком DME посредством интерфейса передачи данных последовательным двоичным кодом. На основе нагрузки, режима работы и данных датчика температуры блок управления двигателем определяет необходимую мощность охлаждения и дает соответствующую команду на блок управления EWPU.
Двигатель насоса охлаждающей жидкости омывается охлаждающей жидкостью системы. В результате двигатель и микросхема охлаждаются.
Подшипники электрического насоса смазываются охлаждающей жидкостью.
При монтажных работах необходимо следить за тем, чтобы насос не работал всухую. При установке насоса после снятия необходимо заполнить его охлаждающей жидкостью. Если насос не будет заполнен охлаждающей жидкостью, постели подшипника могут залипнуть. Впоследствии это создаст проблемы с пуском насоса и тем самым поставит под угрозу работоспособность всей системы охлаждения (невключение насоса приведет к серьезным повреждениям двигателя). Если насос тем не менее работал всухую, то перед завершением монтажа шлангов системы охлаждения следует вручную провернуть внутренний ротор насоса. Сразу после этого следует заправить систему охлаждающей жидкостью.
При монтажных работах необходимо следить за тем, чтобы вилка была сухой и чистой, а разъемы не были повреждены. Диагностические работы разрешается проводить с использованием только рекомендованного переходного кабеля. Следует строго выполнять указания, приведенные в руководстве по ремонту.
Управление теплом
Блок управления двигателем управляет насосом охлаждающей жидкости в зависимости от ситуации: низкая мощность при низкой потребности в охлаждении и низкой температуре наружного воздуха; высокая мощность при высокой потребности в охлаждении и высоких температурах наружного воздуха.
В зависимости от обстоятельств насос охлаждающей жидкости можно даже вообще выключить, например, для быстрого нагрева охлаждающей жидкости при прогревании двигателя. Однако это делается только в том случае, когда не требуется повышенная мощность подогрева и температура наружного воздуха это позволяет.
При регулировании температуры двигателя насос охлаждающей жидкости работает иначе, чем обычные насосы. До настоящего времени термостат мог учитывать только текущую температуру. Программное обеспечение ЭБУ двигателя содержит модель расчета, которая на основании нагрузки может определять динамику температуры головки блока цилиндров.
Система управления теплом теперь позволяет через термостат с программным управлением получать поля характеристик, служащие основой для управления насосом охлаждающей жидкости. Таким образом, ЭБУ двигателя может установить соответствующую температуру двигателя в зависимости от его динамических показателей. Это значит, что могут быть установлены четыре различных диапазона температур:
- 112 °C (Экономичный режим)
- 105 °C (Нормальный режим)
- 95 °C (Режим High)
- 80 °C (Режим High + KFT)
Если на основании динамических характеристик ЭБУ двигателя распознает экономичный режим, регулирующая система стремится установить более высокую температуру головки блока цилиндров (112 °C).
В этом температурном диапазоне двигатель работает с относительно низким расходом топлива, поскольку уменьшается трение в его внутренних деталях.
Повышение температуры также способствует снижению расхода топлива в диапазоне малых нагрузок.
В режимах HIGH и KFT водитель может использовать оптимальную развиваемую двигателем мощность. При этом температура головки блока цилиндров снижается до 80 °C. Это обеспечивает лучшую степень наполнения, что оказывает влияние на повышение крутящего момента двигателя.
ЭБУ двигателя может теперь установить определенный режим работы с учетом ситуации движения. Таким образом, систему охлаждения может влиять на расход и мощность двигателя.
Интеллектуальное управление теплом расширяет возможности двигателя и пользователя
В предыдущем разделе было описано, в каком режиме работы реализовано управление теплом. Электрический насос охлаждающей жидкости предоставляет другие дополнительные возможности.
Так, сейчас стало возможным прогревать двигатель без циркуляции охлаждающей жидкости. Или же давать насосу работать после выключения двигателя, чтобы поддерживать отвод тепла.
В следующей таблице приведены преимущества, которые предоставляет такой насос:
- Расход топлива
- Быстрый прогрев при отсутствии циркуляции охлаждающей жидкости
- Повышенная степень сжатия за счет большей интенсивности охлаждения при полной нагрузке по сравнению с предыдущими двигателями
- Выброс вредных веществ
- Ускорение прогрева за счет снижения скорости вращения насоса (n => 0) и, как следствие, малого охлаждающего потока
- Уменьшение мощности, затрачиваемой на преодоление трения
- Уменьшение расхода топлива
- Снижение показателей выброса ОГ
- Мощность
- Охлаждение деталей независимо от частоты вращения, производительность насоса охлаждающей жидкости в соответствии с потребностью, снижение потерь мощности
- Комфорт
- Оптимальный поток
- мощность обогрева повышается по запросу;
- остаточное тепло при неработающем двигателе;
- Оптимальный поток
- Защита деталей
- Инерционная работа EWP – лучший теплоотвод от горячего выключенного двигателя
Сравнение систем охлаждения с механическим и электрическим насосом охлаждающей жидкости
Обычный насос охлаждающей жидкости
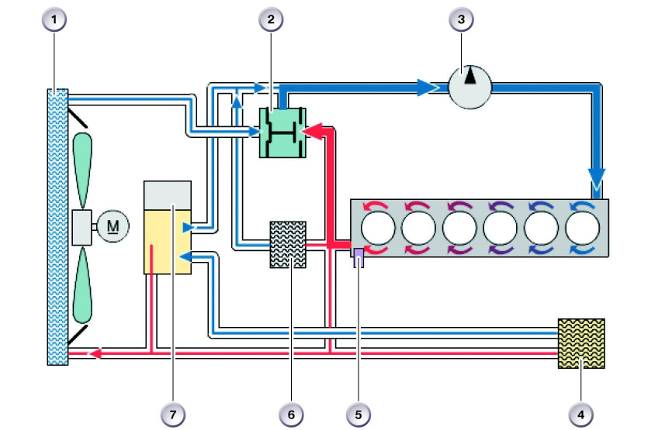
Схема системы охлаждения с насосом охлаждающей жидкости с ременным приводом:
1 – Радиатор; 2 – Программируемый термостат (KFT); 3 – Насос охлаждающей жидкости с ременным приводом; 4 – Теплообменник отопителя; 5 – Датчик температуры на выходе из головки блока цилиндров; 6 – Жидкостно масляный теплообменник (MÖWWT); 7 – Расширительный бачок;

Поток в зависимости от частоты вращения коленвала двигателя:
QV – Расход; nMot – Частота вращения коленвала;
В насосах с ременным приводом интенсивность циркуляции охлаждающей жидкости соответствует частоте вращения коленвала двигателя. Регулировку температуры можно осуществлять только, изменяя расход циркулирующей охлаждающей жидкости с помощью термостата. Термостат переключается между малым и большим контуром, включающим в себя радиатор. То есть, интенсивность охлаждения зависит от частоты вращения коленвала двигателя.
Электрический насос охлаждающей жидкости

Схема системы охлаждения с электрическим насосом охлаждающей жидкости:
1 – Радиатор; 2 – Датчик температуры на выходе из радиатора; 3 – Программируемый термостат (KFT); 4 – Электрический насос охлаждающей жидкости; 5 – Теплообменник отопителя; 6 – Датчик температуры на выходе из головки блока цилиндров; 7 – Жидкостно масляный теплообменник (MÖWWT); 8 – Расширительный бачок;

Регулируемый поток охлаждающей жидкости:
QV – Расход; nMot – Частота вращения коленвала; 1 – Максимальная скорость вращения насоса; 2 – Минимальная скорость вращения насоса;
В системе охлаждения с электрическим насосом охлаждающей жидкости используются как возможности обычной системы, так и новые возможности.
Таким образом интенсивность охлаждения системы теперь может корректироваться в соответствии со свободно изменяемым объемным расходом охлаждающей жидкости.. При прогретом работающем двигателе насос охлаждающей жидкости можно выключить, или же включить его при остановленном двигателе. Как видно на рисунке, благодаря этому создается рабочая зона, в которой можно запросить независимую скорость вращения насоса охлаждающей жидкости. Это зона ограничивается максимальной и минимальной скоростью вращения.
При заливке жидкости и удалении воздуха работники СТО должны соблюдать следующий порядок действий: 1. Залить охлаждающую жидкость через расширительный бачок (AGB). Уровень жидкости довести до нижней кромки AGB. 2. Закрыть AGB. 3. Включить зажигание. 4. Включить максимальный обогрев (температура), вентилятор (самая малая ступень). 5. Нажимать педаль акселератора до отказа в течение как минимум 10 секунд. Двигатель НЕ запускать. 6. Удаление воздуха через EWP идет прибл. 12 минут. После этого проверить уровень жидкости, и при необходимости довести его до отметки MAX. 7. Охлаждающий контур и пробку сливного отверстия проверить на герметичность. 8. Если эту процедуру нужно выполнить многократно, следует полностью выключить блок DME (вынуть ключ зажигания прибл. на 3 минуты), и затем повторить все действия, начиная с пункта 3. При недостаточно заряженном аккумуляторе подключить зарядное устройство.
Трехступенчатая раздельная система всасывания (DISA)
Узел всасывания/DISA состоит из следующих основных частей:
- резонаторная трубка;
- переходная трубка;
- труба резонатор;
- привод DISA 1;
- привод DISA 2;

Впускной коллектор двигателя БМВ Н52:
1 – Впускной коллектор; 2 – Трубы резонаторы; 3 – Резонаторная трубка; 4 – Переходная трубка;
Описание функционирования резонансного наддува
Крутящий момент, развиваемый двигателем, в значительной степени зависит от качества наполнения цилиндров горючей смесью при такте всасывания.
Масса горючей смеси в отдельном цилиндре, поступившая в него при такте всасывания за счет опускания поршня при открытых клапанах, получает колебательное движение. Эти колебания накладываются на колебания, которые возникают при скачках давления, как только приведенная в движение масса смеси в цилиндре начинает подступать к закрывающимся впускным клапанам.
Когда оба колебательных процесса накладываются друг на друга, образуются результирующие колебания – так называемые резонансные колебания. Резонанс может усиливать или ослаблять выходные колебания. Когда в цилиндре в начале такта всасывания возникает скачек давления или его падение перед впускным клапаном, резонанс сильно зависит от пути, который проходят накладывающиеся друг на друга колебания при возвращении в зону всасывания, а также от частоты вращения коленвала двигателя и скорости движения горючей смеси.
Желание добиться высокого крутящего момента в широком диапазоне частоты вращения требует использования все более разнообразных направляющих всасываемого воздуха на двигателях внутреннего сгорания.
Геометрия системы впуска и управление ею также значительно влияют на качество смены горючей смеси в цилиндре.
Впускной коллектор с постоянной длиной обеспечивает оптимальное наполнение цилиндров только при определенной частоте вращения коленвала.
Для этой цели на M54 используется двухступенчатая раздельная система всасывания (DISA) с одной заслонкой DISA. Активизация заслонки DISA осуществляется посредством электромагнитного клапана и предвключенного вакуумного ресивера.
Возможности добиться повышения крутящего момента в определенном диапазоне частоты вращения ограничены. Поскольку максимальная частота вращения N52 достигает 7000 об/мин, то использование прежних двухступенчатых систем всасывания привело бы к уменьшению крутящего момента в среднем диапазоне частоты вращения. Для того чтобы обеспечить создание высокого крутящего момента также и в среднем диапазоне частоты вращения, на N52 используется трехступенчатая система всасывания.
Результат использования этих трех ступеней представлен на следующей диаграмме. Высокий крутящий момент создается во всем диапазоне частоты вращения благодаря трем ступеням включения DISA.

Ступени DISA 1–3 в моторе Н52
Принцип работы основан на переключении впускного коллектора с помощью двух приводов DISA и передаточной трубки в зоне всасывания.
В отличие от предыдущих систем, которые управлялись при помощи разрежения, теперь приводы приводятся в действие электродвигателем. Двигатель и приводы DISA образуют единый узел.
Приводы DISA различаются между собой размерами. Привод DISA 2 находится в передаточной трубке, а привод DISA 1 – во впускном коллекторе перед трубой резонатором.
Ступень 1 – холостой ход/низкий диапазон частоты вращения
На холостом ходу и в нижнем диапазоне частоты вращения приводы DISA 1 и 2 закрыты. Всосанный воздух протекает через дроссельную заслонку в резонаторную трубку. В резонаторной трубке всосанная воздушная масса разделяется и через коллектор и трубы резонаторы подается в отдельные цилиндры. Поэтому три цилиндра каждый раз получают сравнительно большую массу смеси.
Порядок работы цилиндров: 1–5–3–6–2–4

Принцип работы ступени 1 резонансного наддува в N52
Ступень 2 – средний диапазон частоты вращения
В среднем диапазоне частоты вращения открывается привод DISA 2. В этом при мере мы будем исходить из того, что впускные клапаны первого цилиндра только еще закрываются. За счет движения газов на закрывающихся впускных клапанах создается пик давления, который через трубу резонатор и трубу коллектора передается на следующий цилиндр в соответствии с порядком работы. За счет этого улучшается наполнение смесью следующего подлежащего наполнению цилиндра.

Принцип работы ступени 2 резонансного наддува в N52
Ступень 3 – верхний диапазон частоты вращения
В верхнем диапазоне частоты вращения открыты оба привода DISA. И здесь мы будем исходить из того, что впускные клапаны первого цилиндра только еще закрываются. И здесь также используется пик давления перед закрывающимися впускными клапанами. Всосанная воздушная масса проходит через резонансную трубку, передаточную трубку и трубу коллектора.

Принцип работы ступени 3 резонансного наддува в N52
Привод DISA
Заслонка системы DISA образует с приводом единый узел. Привод заслонки системы DISA обеспечивается электродвигателем с редуктором.
Управляющая электроника встроена в привод DISA. Привод DISA управляется посредством сигнала с широтно импульсной модуляцией, поступающего от DME MSV70.
Есть только два возможных положения: заслонки могут быть открыты или закрыты, то есть двигатель при управлении ставит заслонки в крайнее положение.

Привод DISA двигателя N52

Модуль всасывания DISA двигателя N52:
1 – Привод DISA 1; 2 – Дроссельная заслонка;

Модуль всасывания DISA двигателя N52:
1 – Привод DISA 2;
Цифровая электронная система управления двигателем (DME) MSV70
Для расширенных функций тактовая частота процессора была увеличена до 60 МГц.
В двигателе N52 серии E63 используется система DME MSV70 (Siemens).
В случае MSV70 управление VALVETRONIC II встроено непосредственно в блок управления двигателем.
Здесь нет отдельного блока управления для VALVETRONIC, как это было в MEV 9.2 (N46).

Входы-выходы системы управления двигателем MSV70 в Н52:
1 – Блок управления цифровой электронной системой управления двигателем (DME); 2 – Датчик температуры в ЭБУ DME; 3 – Датчик давления окружающей среды в ЭБУ DME; 4 – Главное реле системы DME; 5 – Модуль диагностики течи топливного бака (DMTL); 6 – Встроенная автоматическая система отопления и кондиционирования (IHKA); 7 – Электровентилятор (охлаждение двигателя); 8 – Вентилятор отсека управляющей электроники; 9 – Программируемый термостат; 10 – Подогрев системы вентиляции картера двигателя; 11 – Реле отопителя системы вентиляции картера двигателя; 12 – Нагнетатель добавочного воздуха (SLP); 13 – Реле нагнетателя добавочного воздуха; 14 – Расходомер воздуха HFM для добавочного воздуха (зависит от конкретной страны); 15 – Клапан вентиляции топливного бака (TEV); 16 – Э/магнитный клапан VANOS для распредвала впускных клапанов; 17 – Э/магнитный клапан VANOS для распредвала выпускных клапанов; 18 – Электромагнит системы управления жалюзи радиатора (LKS); 19-24 – Инжекторы; 25 – Реле инжекторов; 26-31 – Стержневые катушки зажигания; 32 – Электрический насос охлаждающей жидкости; 33 – Интеллектуальный датчик аккумуляторной батареи (IBS); 34 – Генератор; 35 – Датчик состояния масла (ÖZS); 36 – Соединение с массой; 37 – PT CAN (шина передачи данных); 38 – Разъем подсоединения DIS; 39 – Реле VALVETRONIC; 40 – Лямбда зонд (контрольный со скачкообразной характеристикой); 41 – Лямбда зонд (регулировочный с постоянной характеристикой); 42 – Лямбда зонд (контрольный со скачкообразной характеристикой); 43 – Лямбда зонд (регулировочный с постоянной характеристикой); 44 – Двигатель VALVETRONIC; 45 – Датчик детонации (цил. 1–3); 46 – Датчик детонации (цил. 4–6); 47 – Датчик эксцентрикового вала; 48 – Пленочный термоанемометрический расходомер воздуха (HFM); 49 – Датчик положения распредвала выпускных клапанов; 50 – Датчик положения распредвала впускных клапанов; 51 – Датчик положения коленвала; 52 – Привод DISA; 53 – Привод DISA; 54 – Дроссельная заслонка с электроприводом (EDK); 55 – Модуль педали акселератора (FPM); 56 – Кнопка SPORT; 57 – Датчик температуры охлаждающей жидкости (сигнал температуры двигателя); 58 – Датчик температуры охлаждающей жидкости (на выходе из радиатора); 59 – Модуль ASC, включая функции: DTC, ABS, DSC; 60 – Выключатель стоп сигналов/выключатель проверки стоп сигналов; 61 – Выключатель сцепления; 62 – Система доступа в автомобиль (CAS); 63 – Датчик разности давления; 64 – Выключатель индикатора давления масла;
Принцип работы цифровой электронной системы управления двигателем (DME)
Цифровая электронная система управления двигателем выполняет следующие задачи:
- Управление зажиганием
- Управление впрыском
- Регулировка VALVETRONIC II
- Регулировка температуры двигателя (программное управление клапаном
термостата) - Регулировка электрического насоса охлаждающей жидкости
- Система управления детонацией
- Регулировка значения лямбда
- Управление вентиляцией топливного бака
- Запрос мощности на блок управления кондиционером для компрессора кондиционера
- Активизация трехступенчатой раздельной системы всасывания (DISA)
- Управление электромагнитом для управления воздушной заслонкой (LKS)
- Управление электрическим модулем топливного насоса
- Система поддержания заданной скорости
- Регулировка генератора
- Система вентиляции картера двигателя с подогревом
- Электронный контроль состояния и уровня масла
- Управление электропитанием (IBS)
- Контроль входных и выходных сигналов
- Расчет эквивалентных сигналов и функций аварийного режима
- Самодиагностика

Блок управления MSV70 двигателя БМВ Н52
Блок управления снабжен разъемом, в котором установлено в общей сложности 7 модулей.
А как смазывается маслом эксентрический вал сервопривода?
так же как и распределительный вал